Bugatti 100P
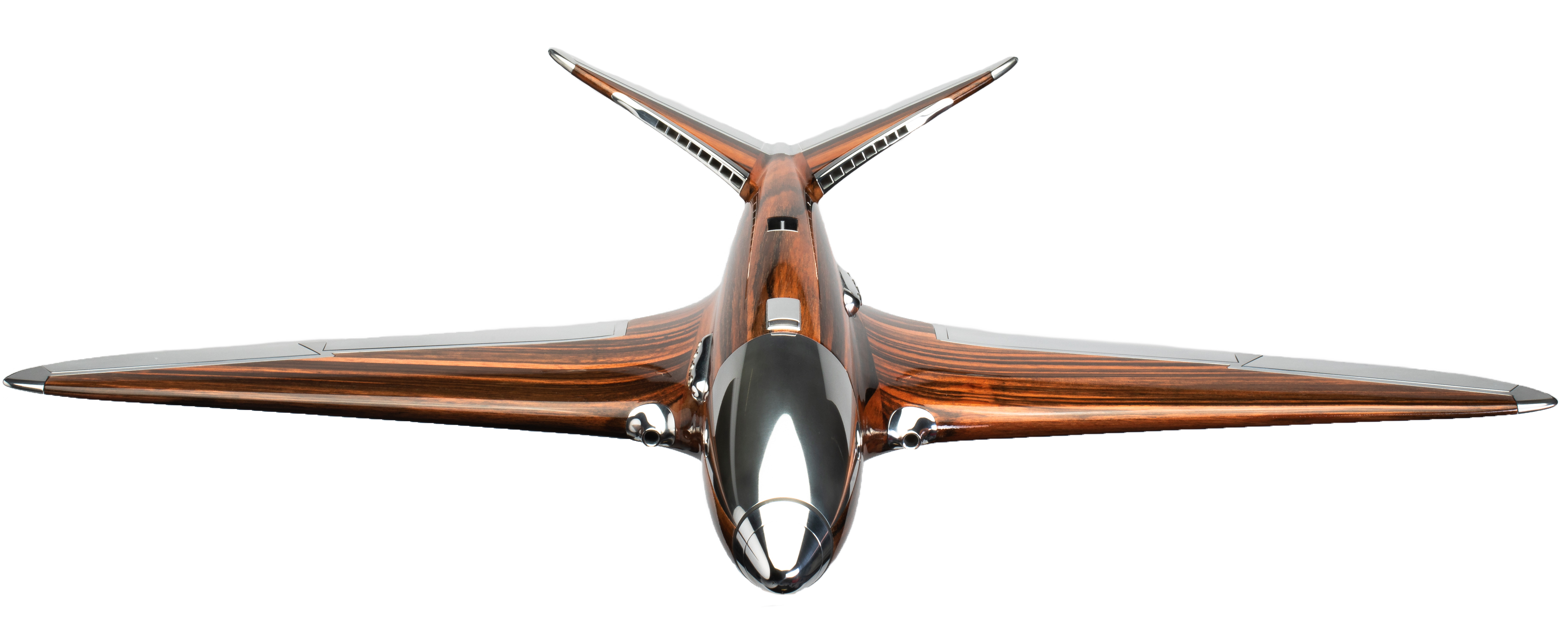
The Bugatti 100P began development in 1937, under contract of the French airforce ministry. Ettore Bugatti had hired the Belgian Louis de Monge as chief engineer of this groundbreaking and complex project. The first version of the airplane was planned for achieving a speed record, with a military version following later.
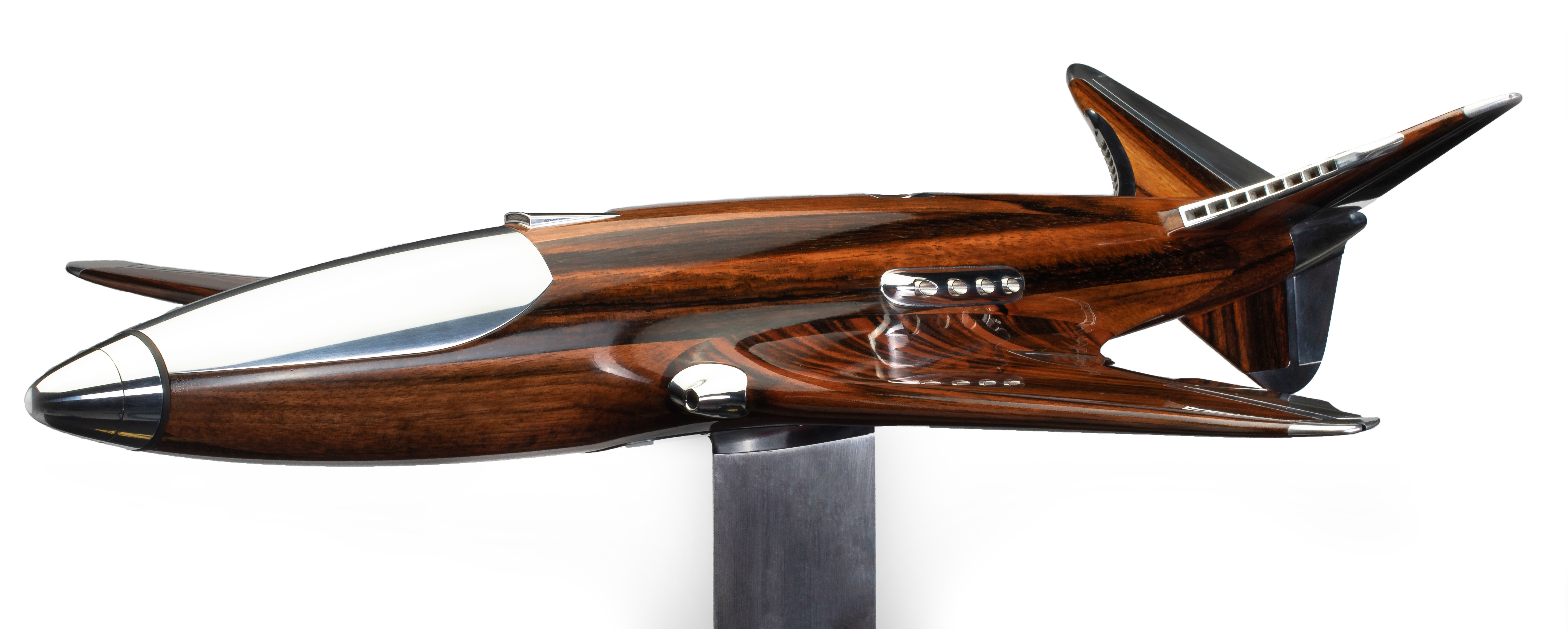
1937
1937
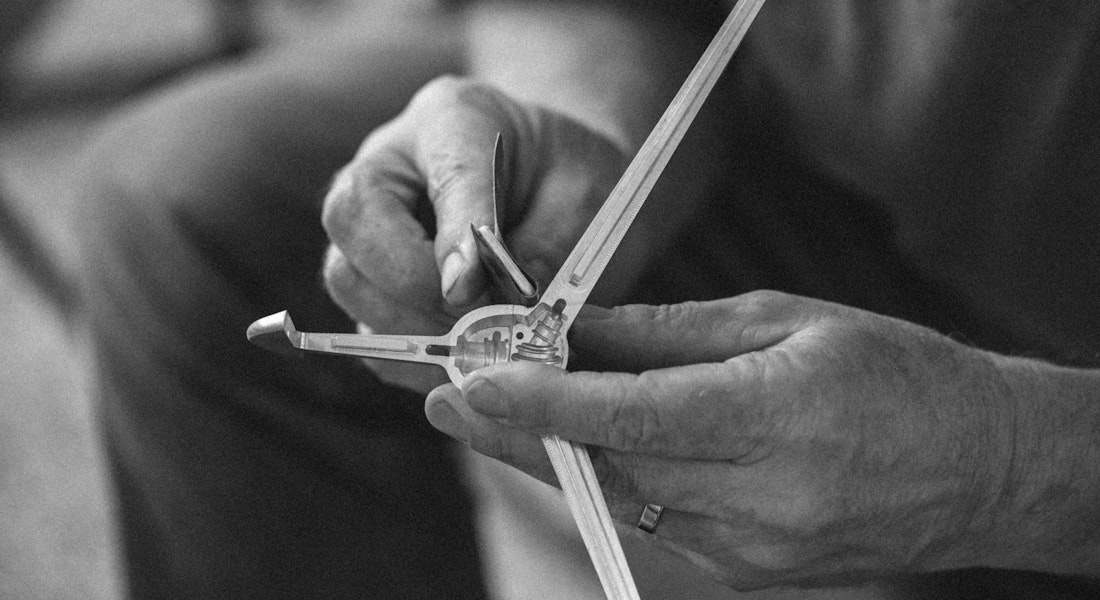
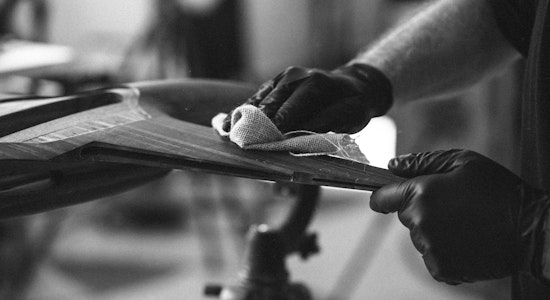
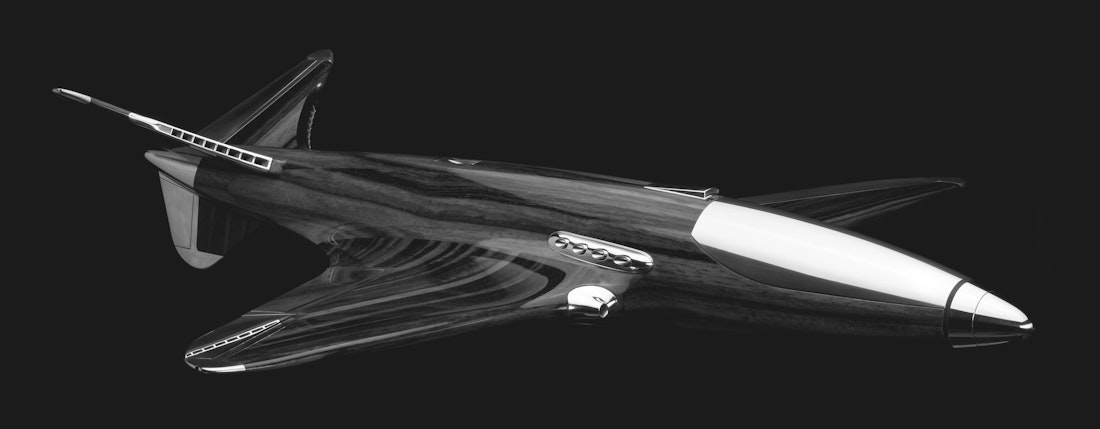
model
This artifact imagines what Bugatti would have built as a sub scale wind tunnel model in the process of optimizing the resulting aircraft. While there is no evidence that he built such a model, it was common during this era to fabricate these sub scale models out of a combination of wood and metal.
In the spirit of wind tunnel models, all of the flying surfaces are articulated and posable. The ailerons include a gearbox that causes them to move in counter directions. The motions include a very satisfying tactile detent provided by an array of precision magnets.
The aluminum on this model is obsessively hand polished to a mirror finish, while wood surfaces are finished with a catalyzed lacquer that is then wet sanded and compounded to produce a piano gloss finish
Only one airplane was produced, but was never finished. This plane still exists, and resides in the EAA museum in Oshkosh, Wisconsin. In addition to being a fabulous art object, these sub scale models exist to help introduce others to this remarkable aircraft design and story.
This example is crafted from hardwood and aluminum in the same way actual mid-century version test articles were.
Machining
Machining
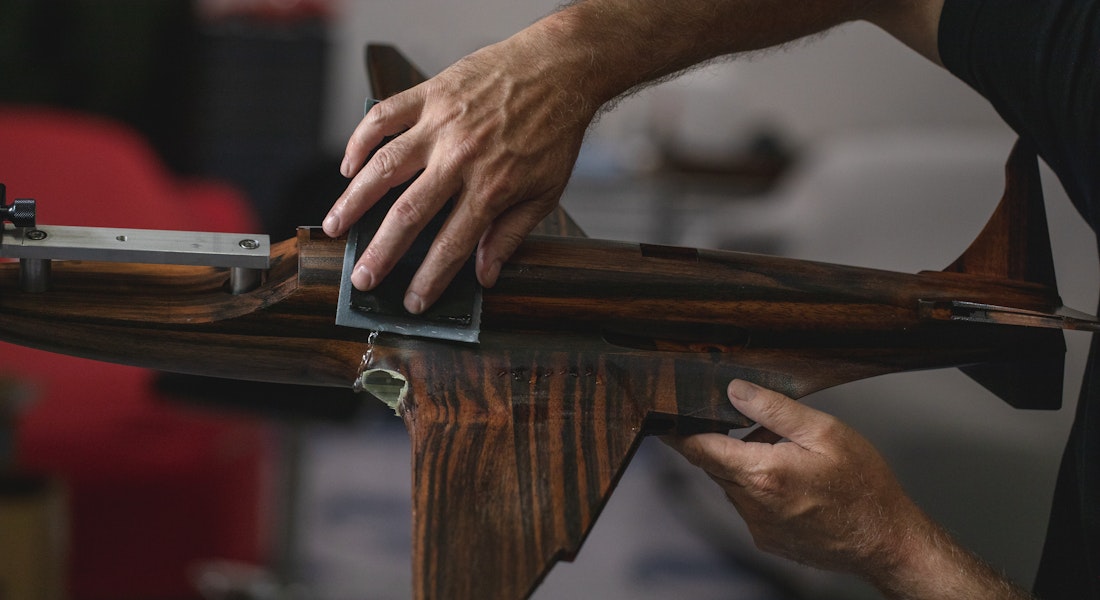
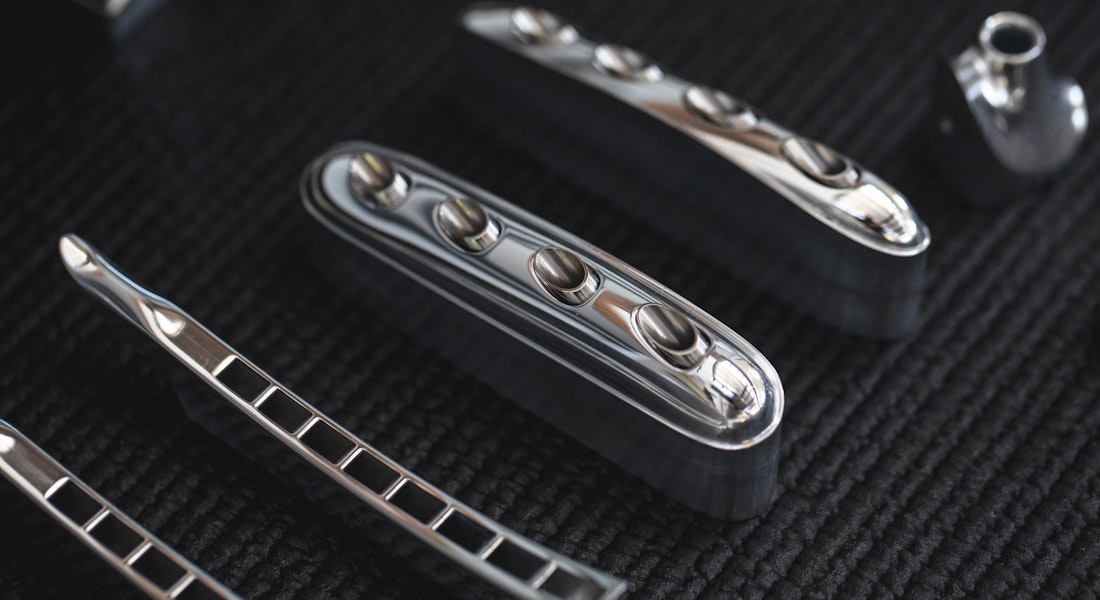
PERIOD-CORRECT
Wood and metal items are constructed from a combination of ebony (selected for its stability regardless of humidity), and aluminum, in the very same fashion of period-correct wind tunnel models.
Aluminum components are polished and coated by a vapor deposition process to create a durable finish that resists fingerprints and staining. The vapor deposition process was chosen to preserve the look of bare aluminum while providing a durable and low-maintenance surface.
Both the wood and aluminum portions of the models are meticulously machined on high-precision 5-axis equipment. Particular attention is paid to the fit and finish of each part. Following the machining process, the wood components are carefully sanded by hand to accept multiple coats of clear catalyzed lacquer. This surface is subsequently wet sanded and wet polished.
Purchase Form
Purchase Form
See our full collection of products. Choose the material types, view detailed specs and pricing, and submit your order. see products>